全球最大碳纤维增强热塑性复合材料机身(MFFD)顺利制造完成
近日,德国弗劳恩霍夫制造工艺与应用材料研究所(IFAM)宣布,其与合作伙伴已联合完成的热塑性复合材料机身演示验证件(MFFD)完成上下机身的左右焊缝连接,并将8×4米的全尺寸部件发送至位于德国汉堡的应用航空研究中心与机舱顶部模块件集成并进行测试。
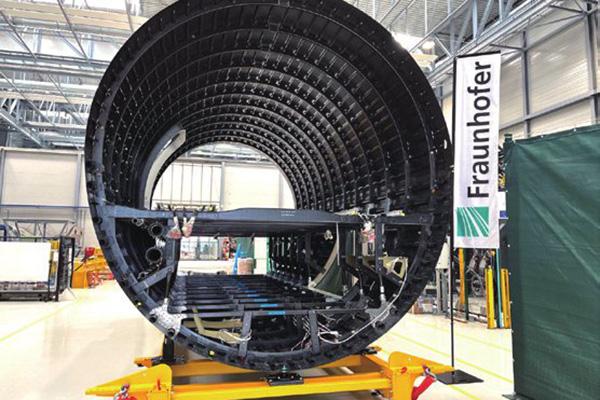
MFFD被认为是世界上最大的碳纤维增强热塑性复合材料(CFRTP)飞机机身部件,代表了一种以1:1比例展示热塑性复合材料飞机机身自动化制造的新模式。该项目中使用的材料和制造技术,可在高速生产过程中减轻约10%的结构重量并降低10%的成本。
作为“智能多功能集成热塑性复合材料机身”(STUNNING)项目的一部分,热塑性复合材料下机身壳体在高温高压下条件经热压罐固化成型,由GKN Fokker、Diehl航空、荷兰航空航天中心(NLR)和代尔夫特理工大学组成的团队共同完成。
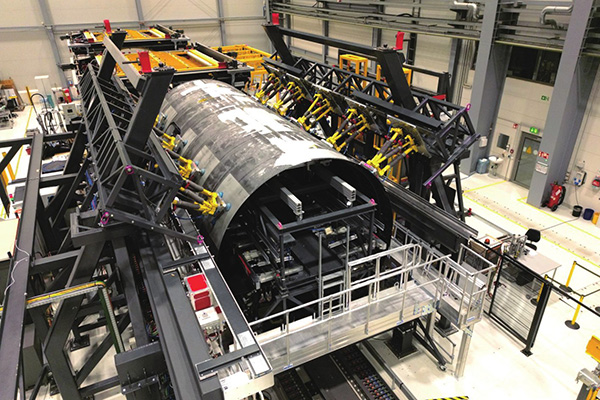
热塑性复合材料上机身壳体采用纤维带铺放和原位固结工艺制造,由Premium Aerotec、空客、Aernnova和德国航空航天中心组成的联合团队共同完成。上、下机身壳体均具有高度预集成度,采用几乎无铆钉的架构设计,与现有传统机身相比重量减轻10%。
MFFD是继2021年顺利完成“自动化客舱和货舱衬里装配方法”(ACCLAIM)项目中自动化客舱装配1:1比例平台之后,弗劳恩霍夫研究所做出重大贡献的第二个“洁净天空2”大型演示验证项目。MFFD热塑性复合材料机身部件已运往位于德国汉堡的应用航空研究中心(ZAL),并在那里最终完成机舱顶部模块的集成。随后,整体部件将用于进一步测试和演示验证。